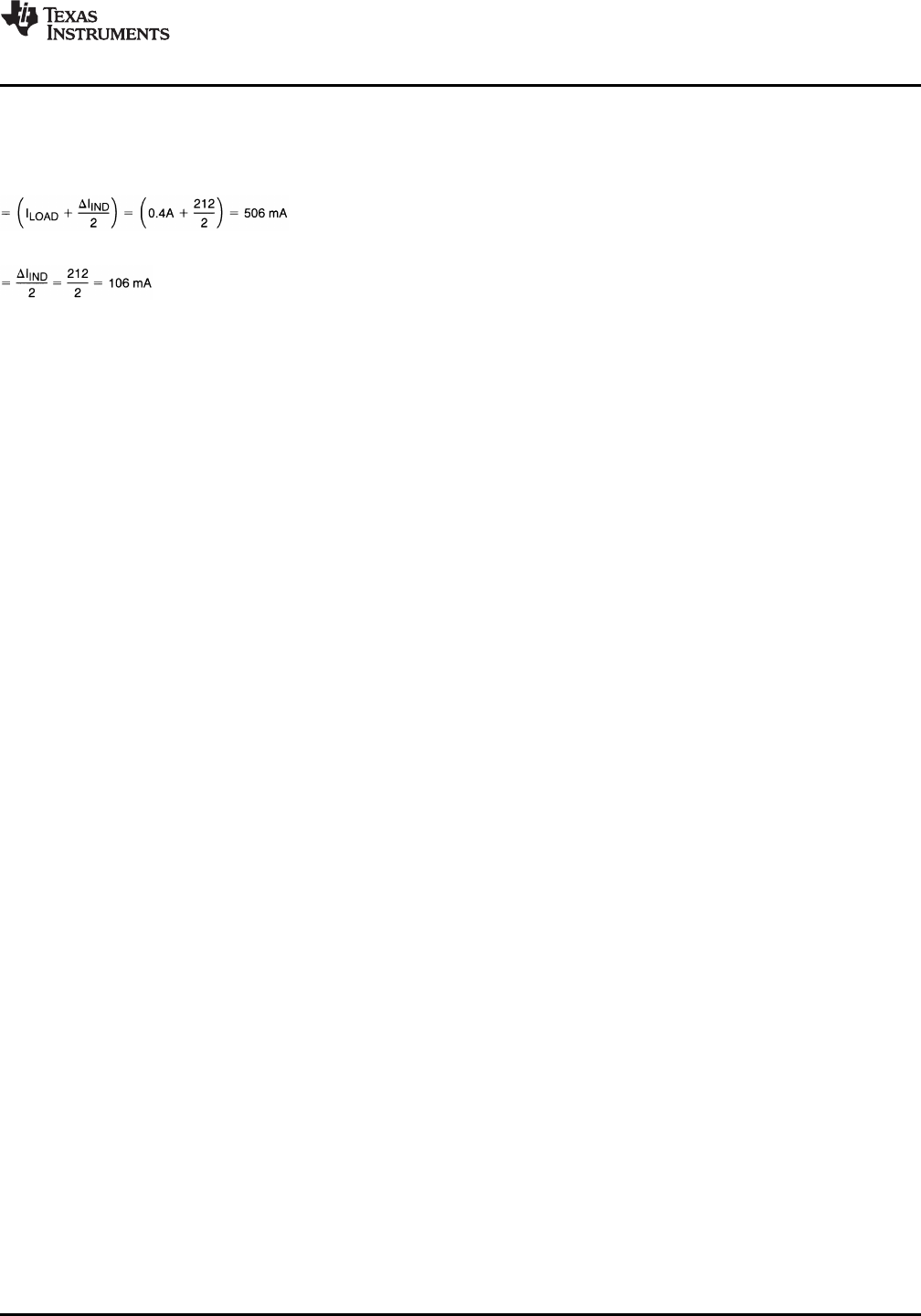
LM2574, LM2574HV
www.ti.com
SNVS104C –JUNE 1999–REVISED APRIL 2013
From the previous example, the Peak-to-peak Inductor Ripple Current (ΔI
IND
) = 212 mA p-p. Once the Δ
IND
value
is known, the following three formulas can be used to calculate additional information about the switching
regulator circuit:
1. Peak Inductor or peak switch current
(2)
2. Minimum load current before the circuit becomes discontinuous
(3)
3. Output Ripple Voltage = (ΔI
IND
) × (ESR of C
OUT
)
The selection guide chooses inductor values suitable for continuous mode operation, but if the inductor value
chosen is prohibitively high, the designer should investigate the possibility of discontinuous operation. The
computer design software Switchers Made Simple will provide all component values for discontinuous (as well
as continuous) mode of operation.
Inductors are available in different styles such as pot core, toroid, E-frame, bobbin core, etc., as well as different
core materials, such as ferrites and powdered iron. The least expensive, the bobbin core type, consists of wire
wrapped on a ferrite rod core. This type of construction makes for an inexpensive inductor, but since the
magnetic flux is not completely contained within the core, it generates more electro-magnetic interference (EMI).
This EMl can cause problems in sensitive circuits, or can give incorrect scope readings because of induced
voltages in the scope probe.
The inductors listed in the selection chart include powdered iron toroid for Pulse Engineering, and ferrite bobbin
core for Renco.
An inductor should not be operated beyond its maximum rated current because it may saturate. When an
inductor begins to saturate, the inductance decreases rapidly and the inductor begins to look mainly resistive (the
DC resistance of the winding). This can cause the inductor current to rise very rapidly and will affect the energy
storage capabilities of the inductor and could cause inductor overheating. Different inductor types have different
saturation characteristics, and this should be kept in mind when selecting an inductor. The inductor
manufacturers' data sheets include current and energy limits to avoid inductor saturation.
OUTPUT CAPACITOR
An output capacitor is required to filter the output voltage and is needed for loop stability. The capacitor should
be located near the LM2574 using short pc board traces. Standard aluminum electrolytics are usually adequate,
but low ESR types are recommended for low output ripple voltage and good stability. The ESR of a capacitor
depends on many factors, some which are: the value, the voltage rating, physical size and the type of
construction. In general, low value or low voltage (less than 12V) electrolytic capacitors usually have higher ESR
numbers.
The amount of output ripple voltage is primarily a function of the ESR (Equivalent Series Resistance) of the
output capacitor and the amplitude of the inductor ripple current (ΔI
IND
). See INDUCTOR RIPPLE CURRENT
(ΔI
IND
) in Application Hints.
The lower capacitor values (100 μF- 330 μF) will allow typically 50 mV to 150 mV of output ripple voltage, while
larger-value capacitors will reduce the ripple to approximately 20 mV to 50 mV.
Output Ripple Voltage = (ΔI
IND
) (ESR of C
OUT
)
To further reduce the output ripple voltage, several standard electrolytic capacitors may be paralleled, or a
higher-grade capacitor may be used. Such capacitors are often called “high-frequency,” “low-inductance,” or
“low-ESR.” These will reduce the output ripple to 10 mV or 20 mV. However, when operating in the continuous
mode, reducing the ESR below 0.03Ω can cause instability in the regulator.
Tantalum capacitors can have a very low ESR, and should be carefully evaluated if it is the only output capacitor.
Because of their good low temperature characteristics, a tantalum can be used in parallel with aluminum
electrolytics, with the tantalum making up 10% or 20% of the total capacitance.
The capacitor's ripple current rating at 52 kHz should be at least 50% higher than the peak-to-peak inductor
ripple current.
Copyright © 1999–2013, Texas Instruments Incorporated Submit Documentation Feedback 19
Product Folder Links: LM2574 LM2574HV